FAQ’s 2020
About IEC Thermo
IEC Thermo is the world’s leader in hemp drying solutions. We have been providing and manufacturing industrial scale, continuous feed dryers since 2009, with multiple successful projects in the dairy, poultry, and wood pellet industries. Prior to that, we engaged in process engineering work with Feeco International and Allis Chalmers (which was acquired by Svedala and then Metso Minerals), working to further hone the developmental and process technologies in use today. The culmination of these experiences led to the design and installation of the first large scale hemp dryer for GenCanna in 2016. As long-time leaders in the hemp drying industry, we have more drying experience than anyone else in the biomass market space, and we look forward to working to make your drying project a profitable endeavor.
Questions about an IEC H.E.M.P. Dryer
Where do the IEC Thermo H.E.M.P. Dryers components come from?
Our components are 100% manufactured in the U.S.A.!
Why dry with an IEC Thermo H.E.M.P. Dryer?
Successful growers and processors have come to realize that profitable large scale operations are dependent upon minimal labor inputs and continuous feed dryer systems. Hang drying, small batch drying, or other processes requiring high temperatures and manual labor are not feasible business plans with a unique agricultural product like hemp. One must be able to rapidly dry and stabilize large volumes of biomass for future processing, whether that is classifying the dried products, pelletizing, or warehousing product for future extraction and utilization. IEC Thermo H.E.M.P. Dryers are the only dryers able to take you from harvested or baled material to a dried, stabilized product in under two minutes; all while maintaining the CBD cannabinoids and other cannabinoid profiles, and all at the lowest temperatures of any hemp drying system available today.
How does the IEC Thermo H.E.M.P. dryer work?
The IEC Thermo H.E.M.P. dryer utilizes a two-stage drying process for the rapid removal of moisture from the biomass (hemp). This ultrafast convection process protects the cannabinoids as the drying process is facilitated by mixing high speed air, warmth, and infeed particles. Using large fans, we pull the hemp particles through a flash dryer in the first stage of the dry down, and then a fluid bed dryer is utilized in the second stage of the process. The combination of these drying techniques is what allows us to protect the cannabinoids and process the crop at a scale that is unprecedented in the industry. When feed meeting system specifications is utilized, the material never stops moving in the system and a continues drying flow is achieved.
What is the maximum temperature the biomass will reach in and IEC Dryer, and for how long?
Typical maximum exposure temperatures in an IEC Dryer are 130-140℉, and this exposure is around 20 seconds. The entire drying cycle typically lasts 60-120 seconds depending on feed, moisture content, ambient air temperatures, and operating proficiency.
Do IEC Dryers decarboxylate hemp?
No, IEC Dryers do not decarboxylate hemp. The time needed to facilitate decarboxylation is generally 20 minutes or more, with sustained temperatures of 220℉ or higher for the entire period. While the air temperature in and IEC Dryer gets above 600℉ at certain points in the system, the biomass (hemp) never gets above 130-140℉. The average dwell time for product traveling through our dryer system is 90 seconds, so minimal to no decarboxylation of the hemp occurs. For further information on decarboxylation, please reference: (https://www.cbdschool.com/what-is-decarboxylated-cbd/)
What are the typical capacities of an IEC H.E.M.P Dryer?
Typical Input (feed capacities going into the system are):
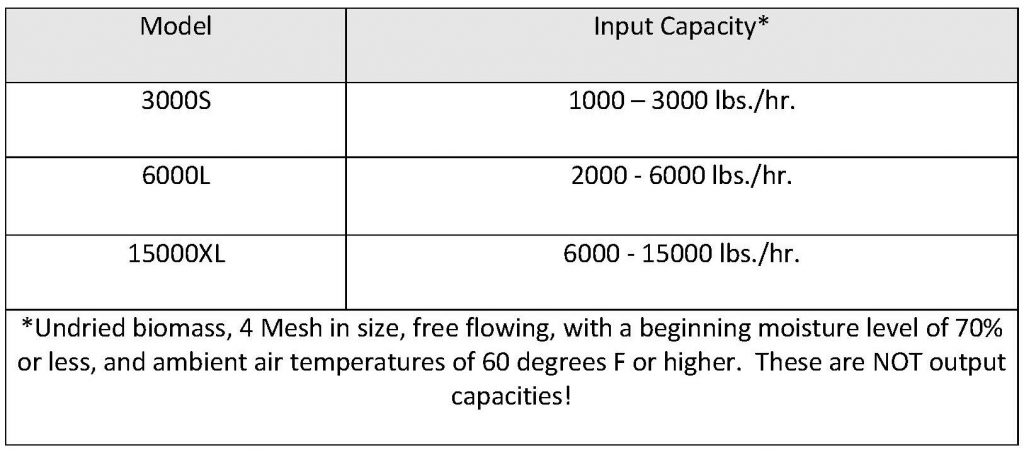
Are the input and output capacities for an IEC H.E.M.P. Dryer the same number- am I loosing product?
No, the input pounds per hour typical capacities and the output of dried material number are not the same number. Feed input (hemp/ biomass with an assumed moisture level of 70%) going into the system contains particles of hemp to be dried, and water inside the green or baled material. As the biomass travels through the dryer system, water is removed (product is dried). Therefore, under normal operating conditions with proper feed (60℉ ambient air temperatures, low humidity, biomass moisture levels of 70% or less, feed size of #4 Mesh that is free flowing and discrete), you may be able to feed up to 6,000 pounds per hour in a 6000L dryer system and get 1,800 pounds of dried product out (assuming a 70% moisture level of biomass). Hemp is not degraded, CBD oil is not lost, only water has been removed (6,000 pounds of feed, removing 70% moisture- 4,200 pounds, yields 1,800 pounds of dried material).
How do I select the right size Dryer for my needs?
Ultimately, it is the buyer’s responsibility to adequately determine the best system for present and future drying needs. Best practices would be to assess typical Dryer capacities for production and assume the low end of those capacities as your starting point. For example, if you need to dry at least 6000 lbs. per hour you should not select the dryer with the max input of 6000 lbs. per hour. Instead you should select the larger capacity unit that always meets your low-end minimums and provides increased output as you master the system. In this case, a 6,000 lbs. per hour need would dictate the purchase of a 15000XL Dryer unit.
Does IEC make a Dryer system larger than the 15000XL?
No. Systems larger than the 15000XL require special accommodations for fabrication, shipping, and assembly, all of which add substantial costs to the project cost. For capacities larger than 15,000 lbs. we recommend you consider multiple systems to allow for capacity and variables in feed conditions.
Questions about proper feed for an IEC H.E.M.P. Dryer
What kind of feed can I put in the IEC Dryer system?
Feed is the most important part of the drying process (any drying process), but especially so with a convection system like the IEC H.E.M.P. Dryer (the drying is accomplished by solids mixing with high speed, warm air). The better the feed, the better the air and particle mixing, and the more efficient the drying process will be. Clients who account for this often meet or exceed their drying expectations, and significantly increase the profitability of their operations.
Feed material for the dryer should be able to pass through a #4 Mesh screen (or roughly 1/4″ pieces). It is imperative that the feed material consist of free flowing, discrete solids (like flakes of Oregano), free of: entanglements, wet or dry clumps of material, fiber (holding large masses together), chunks of ice or frozen material, dirt, rocks, roots, stems, metal pieces, and biomass with excessive moisture (above 70%).
What happens if out of specification feed is put into an IEC Dryer system?
If feed material that does not meet specifications (feed material that is overly resinous, wet, clumpy, frozen, too large- more than #4 Mesh, fibrous, etc.) is “dried”, the feed material will likely collect within the dryer system and will reduce input/ output capacities. In some cases, these materials may accumulate and create a combustion risk (giant hash bricks in the ducting, excessive fiber collected in the fluid bed or cyclones, etc.).
What variables can affect the typical capacities of the system?
The most important variable is FEED. To reach the maximum input capacity for your system, the feed material must be within the specifications as outlined in all our proposal and marketing materials (discrete, free flowing particles able to pass through a #4 Mesh screen). Larger size particles bound together with fiber, water, ice particles, dirt, etc., will significantly reduce the input capacities of the dryer- and further conditioning or processing of the feed material may be needed before it can enter the Dryer system. Other factors including feed material shape, ambient air temperatures and relative humidity will also affect the input (air temperatures below 60℉, high humidity). Adjusting to the conditions present at your operation is essential to reaching typical capacity ranges. Insulating the ductwork and pre-warming the system in colder temps (30 minutes to 1 hour) may also improve typical capacities, as will general knowledge and experience running the system with your particular crop, operating environment, and feed material.
Does feed effect Dryer system maintenance?
Yes, feed does effect Dryer system maintenance and the Dryer system equipment MUST be maintained and cleaned regularly (frequency depends on feed, ambient air conditions and temperatures, weather, humidity levels, etc.). It is imperative that the dryer operators constantly monitor feed material and inspect the dryer system to ensure build up does not occur anywhere in the system. Special attention should be focused on the J Pipe feed unit, pre dryer ducting, and the fluid bed, all while overseeing the rest of the dryer system during operation. Feed that does not meet proper specifications should not be dried. Other wear/ maintenance items include the airlock wipers, augers (belts & motors), conveyors (belts & motors), the control panel, VFDs, and other critical components for operation (all covered in detail with our operations manual), must be inspected, adjusted, or replaced as needed.
NOTE: For proper system functioning, it is imperative that the feed material be no larger than #4 Mesh in size, and that the biomass particles be discrete and free flowing. Other critical variables to drying success and output rates include: The moisture content of the particles to be dried (70% or drier is ideal), ambient are temperatures, the temperature of the harvested or baled material, and outside weather conditions (especially rain and snow). As stated above, neglecting to utilize proper feed and account for operating conditions may result in negative outcomes when running the Dryer system.
Questions about the startup and operation of an IEC H.E.M.P. Dryer System
What needs to be ready before I can commission my system?
All permitting and equipment assemblies should be completed prior to any commissioning (IEC Thermo is not responsible for any permitting). Once assemblies have been completed, it will be necessary for the client to schedule and oversee the final connections for electrical and gas (gas connections to burners, electrical to the control panels and motors, etc.). One should allow 2-4 weeks for your electrical and gas contractor work to be completed. IEC Thermo Project Managers must be notified by you to confirm connections. Upon confirmation of permitting and final utility connections, an IEC commissioning team will be scheduled for the initial lighting of the burners and to ensure the system is operational. NOTE: Commissioning of the systems (2 days on location) may be scheduled during the months of December through August. No commissioning will take place during the harvest season- so plan accordingly. The commissioning team will NOT dry any hemp material during commissioning. NOTE: Commissioning is NOT training. We are not there to run product during commissioning!
What about training for my employees?
Following the successful commissioning of your dryer system, IEC Thermo will schedule a training team to impart the knowledge needed to safely run our Dryer system. The training team will be onsite for three days to complete the training curriculum, and hemp/ biomass may be dried. It is highly recommended that the purchaser of the Dryer system send at least 2 individuals to our training center in Northern Illinois once the initial equipment deposit has been made- do NOT wait until the harvest season to initiate training. During the months of September through December, field training slots will be extremely limited, so take advantage of the off-season availability.
When can I expect to be at typical Dryer capacities?
We recommend you allow 4-6 weeks to fully calibrate the settings of the Dryer system and get used to the controls and equipment. This allows your operators to learn to adjust for the conditions present at your facility before starting to realize the potential of the Dryer. Each site is different, with variations in harvest equipment, hemp feed, moisture, humidity, and ambient temperatures all contributing to the operation of the Dryer- and all these factors must be accounted for before typical capacities can be achieved.
The dryer is only one component of your process (it is not the process). Be sure you consider matching your harvest and storage capacity to the Dryer needed to accomplish your business goals, and make sure proper training on planting and harvest techniques have taken place prior to drying any product.
How many employees will I need to operate the dryer?
We recommend a minimum of four (4) to five (5) employees to operate the dryer. The feed input, feed output, fluid bed, and system controls should always be monitored when the system is in operation. Failure to use the recommended number of operators could result in the Dryer system clogging, creating the potential for buildup of combustible materials in the system. Please account for 1-2 of the designated operators to perform daily maintenance and cleanout of critical components. Failure to properly clean and maintain all portions of the Dryer system will result in equipment failures and reduced capacities.
How long does it take to start and stop the dryer?
The IEC H.E.M.P. Dryer has a programmable PLC so you can create custom sequences based on your specific operations. Typically, initial startup and complete shutdown times average 2-5 minutes. When operating the system at ambient air temperatures of 60℉ or high, Dryer system temperatures may stabilize more quickly, and feed may be introduced into the system within 15-30 minutes. During colder temperatures, or when feeding product that is baled, it may be necessary to warm the system for up to 1 hour prior to the introduction of feed. Feed quality, moisture levels, and ambient temperatures all dictate, and effect system start up times.
Is it difficult or dangerous to operate the dryer?
The IEC Thermo Dryer system is a large-scale agricultural piece of equipment, with moving parts, burners and flames present. While it is not inherently difficult or dangerous to operate, it does require training, proper operation, attention to the system, daily cleaning, and daily maintenance. Those not willing to operate the system within specified guidelines (specified feed size of #4 Mesh, free flowing and discrete particles, etc.), do so at their own risk, and IEC assumes no liability for improper feed or operation.
Is maintenance required with an IEC Dryer system?
The Dryer system equipment MUST be maintained and cleaned regularly (frequency depends on feed, ambient air conditions, weather, humidity levels, etc.). It is imperative that the dryer operators constantly monitor feed material and inspect the dryer system to ensure build up does not occur anywhere in the system. Special attention should be focused on the J Pipe feed unit, pre dryer ducting, and the fluid bed, all while overseeing the rest of the dryer system during operation. Feed that does not meet proper specifications should not be dried. Other wear/ maintenance items include the airlock wipers, augers (belts & motors), conveyors (belts & motors), the control panel, VFDs, and other critical components for operation (all covered in detail with our operations manual), must be inspected, adjusted, or replaced as needed.
NOTE: For proper system functioning, it is imperative that the feed material be no larger than #4 Mesh in size, and that the biomass particles be discrete and free flowing. Other critical variables to drying success and output rates include: The moisture content of the particles to be dried (70% or drier is ideal), ambient are temperatures, the temperature of the harvested or baled material, and outside weather conditions (especially rain and snow). As stated above, neglecting to utilize proper feed and account for operating conditions may result in negative outcomes when running the Dryer system.
What are your service and training rates if we need to schedule additional field visits?
IEC Thermo offers complete technical support services and training. Our training rates vary based on the level and scope of training. Please contact IEC Thermo for a current rate sheet and proposal for training or system service.
Questions regarding the purchase & assembly of an IEC H.E.M.P. Dryer
What does the IEC Thermo H.E.M.P. Dryer include?
The physical equipment needed to successfully dry biomass, as spelled out in the client’s Equipment Proposal. Unless otherwise specified, it may also include ductwork and assembly pricing. Commissioning of the system and Training is also included. Note: Permitting, utility connections, site preparation, equipment unloading at your site, and final utility connections are Not included in the proposal nor are part of the purchase of an IEC Dryer system.
If IEC Thermo provides assembly is the system “Turnkey”?
IEC Thermo H.E.M.P. Dryer systems are NOT sold as “Turnkey”. IEC is only setting and assembling the equipment IEC has sold. To complete the Dryer system project the client will be responsible for having a contractor make all gas and electrical connections (initial to location and final hookup to equipment), along with local permitting. The client is also responsible for contracting and managing any building permits, construction of facilities, concrete work, etc. IEC Thermo is only responsible for providing the Dryer equipment as specified in our Proposal and Terms & Conditions of Sale.
What support is included with the IEC Thermo H.E.M.P. dryer?
There are three elements to the IEC Thermo approach in getting your Dryer system up and running. They are the assignment of a Project Manager, Commissioning, and Training.
Upon receipt of your initial deposit, IEC will assign a Project Manager to your account. This individual will be there to offer you guidance and answer questions. Most importantly, the Project Manager is there to coordinate the behind the scenes operations for your project (scheduling assembly crews, commissioning, training, and project completion). The IEC Project Manager is NOT the general contractor of your project, nor are they responsible for overseeing the work that needs to be completed bring about project success. Missed commissioning dates are not the responsibility of IEC Thermo.
Once we have confirmed you are ready to start your system, we will schedule a commissioning team to be onsite for two working days to light the burners and make the system operational. They will not run hemp material at this time, nor conduct training. Commissioning may be scheduled from December through August, with no commissioning occurring during the harvest season.
Upon completion of the commissioning phase, and when you have hemp/ biomass material available, we will schedule a training team to train staff on dryer operations. We will be onsite for three working days to complete our training curriculum with your trainees and operators. Included are the travel costs to get our teams to your location, room, and per diem expenses for that representative.
What are typical delivery times on Dryer systems?
Generally, equipment ships within 14-18 weeks after we receive your deposit and the final payment has been realized. NOTE: Once final payment is made, the equipment will ship immediately to your location- whether that be a field, barn, or completed building. IEC will coordinate shipping details with your staff, but it is your responsibility to safely offload and store all equipment IEC ships to the location prior to assembly and commissioning.
What kind of equipment do I need to have on site to receive my equipment shipments?
You will be receiving large scale industrial equipment. For the 3000S, 6000L and 15000XL dryer systems you will need an 8000 lbs. capacity forklift (all terrain if not an improved facility) with Fork Extensions, a 20 ft. chain, a 12,000 lbs. capacity Telehandler (or crane), and a clevis pin on hand to accept the drying system components. Please anticipate 5-7 flatbed loads of supplies to reach your destination, and plan on a ½ to a full day to unload the equipment and store it safely. Delays in unloading, damage to equipment during unloading, and any resultant fees are the responsibility of the client.
What is the buyer responsible for prior to the pre-assembly?
The purchaser of the IEC Thermo H.E.M.P. Dryer system will be responsible for providing any required local permits, a local gas contractor to prepare and connect the gas or propane for the system burners, and a local electrician to prepare and connect the electrical system. Site-specific rules and regulations prohibit IEC Thermo from providing these services. Be aware that these are commercial level connections, so be sure to select contractors with the appropriate experience. They should begin work on the project as soon as possible to ensure completion dates.
How long will assembly take at my facility?
If you have properly prepared the site (building, permitting, electrical, gas, etc.) assembly can generally be completed in 10-16 days. Following assembly, utility connections must be completed prior to scheduling commissioning. Commissioning must be completed prior to any onsite training. Please allow for 2-4 weeks for electrical and gas contractors to complete their work. Based on experience- it will take a lot longer than you think so plan accordingly.
If I need to pour a concrete pad, how thick does it need to be?
This is a question for your concrete contractor or a civil engineer, as soil types, dynamic loads, and static loads are different for each application. Individual weights of the components are available upon request so that your contractor can help advise you in your decision.
How tall does my building need to be?
We have the “minimum height” requirements in the technical section for each of our systems: The 3000S, 6000L, and 15000XL. It is the sole responsibility of the purchaser to make sure your building (new or existing), will accommodate the equipment you are purchasing from IEC (this also includes doorways, docks, fields, or any other area you need to unload the equipment you purchased for assembly).
How large should I make my concrete pad or building?
We have included “suggestions” for the bare minimums of each of our systems on the specification sheet for the 3000S, 6000L, and 15000XL. These “suggestions” do not account for the storage of raw materials (harvested super sacks of hemp or bales), finished product storage, forklift traffic, human traffic, or other equipment storage. It is the responsibility of the purchaser to provide adequate space for your plant layout. A civil or industrial engineer may be helpful in determining the space for your layout (both present and projected growth).
Questions about Safety
What kind of safety materials are provided?
With every IEC Dryer, we include a “safety kit,” including safety signs, etc. However, it is the client’s responsibility to institute safe work practices surrounding their dryer and other work processes. Please keep in mind that some states have their own “OSHA” equivalent regulatory agencies. We recommend you consult local fire and safety professionals to ensure you are providing adequate hazard controls.
Safety MUST also include a working knowledge of the feed specifications for the system, cleaning of the system components (daily, or more often if needed), and proper maintenance of critical components. A properly staffed location with trained individuals capable of monitoring feed, controls, pre-dryer, fluid bed dryer, conveyors, and output parameters of the Dryer system must also be considered.
What safety training does IEC provide?
The IEC Thermo Operations Manual covers needed safety information. Our Initial Start-Up Training will cover important safety information, too. Employers are responsible for providing employees with needed safety training, and any documentation to ensure the Dryer system is being operated by competent individuals.